Design change
1. When receiving the customer's specification change, the production management center must be asked to reply to the material and scheduling status as soon as possible, and the specification engineer should evaluate the feasibility with the section head/supervisor. If feasible, a new version of the specification table (such as 1.1/1.2, etc.) should be developed, and the original version of the specification table must be retained.
2. Indicate whether to change immediately or in sequence. If the change is not feasible, immediately contact the Business Department for relevant business processing. Unless it is verified by the production management that it will not affect the normal production and will not cause dead materials, it is not allowed to change immediately, because the problem of dead warehouse and the loss caused by rework must be taken into account.
3. The contents before and after the change must be clearly indicated on the expression of the design change. The change notice of the ERP BOM must also indicate the content of the change. The sample or form department of the change must be provided to the material control/quality inspection/specification/order/supplier at the first time. 4. Finally, submit the changed data to the document management department for classification and storage in the file bag of the corresponding customer
Electric vehicle helmet Manufacturer's manufacturing process
1. Printing process:
Original computer plate making output film - printing, development and drying inspection
Revision
On machine printing surface treatment, paper mounting, die-cutting, binding, packaging, sample delivery
Printing order from light to dark: white, yellow, orange, green and red In the process of purple blue silver black printing, the orthographic printing sequence is from light to deep (the substrate is usually T-shirt, circuit board and other opaque materials). In the process of printing, the reverse printing sequence is from deep to light (generally the substrate is PC PVC and other transparent materials)
2. Injection molding process Injection molding extrusion blow molding machine molding semi-finished products will be printed suction cut into four processes
ABS
There are one or two semi-finished product item numbers starting with 2
Integrated molding
There are one, two or three semi-finished product part numbers starting with 2 (EPS group and shell share one code
One code is used for the internal configuration order in EPS group
7、 Use of Bill of Materials
1. Concept of BOM
BOM (Bill of Material), also known as product structure table, product structure tree, part list
2. Functions of BOM
Improve the accuracy of the efficiency of the product material list, avoid the phenomenon of wrong purchase and wrong use of materials, and improve the control of excessive consumption of materials during product production to correctly estimate the standard cost of products
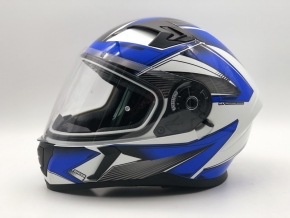